It is essential processes in the manufacturing and packaging of salty snacks. It helps in product traceability, compliance with regulations, and critical information about the product for the customers.
Let’s first talk about the Importance of Marking and Coding on any product.
For Traceability:
If in case a business has to recalls, there product with the help of marking and coding it can be done effectively and ensure consumer safety. With the help of marking and coding, manufacturer can trace each batch of products back to its origin. It helps quickly to identify and address any issues related to contamination or defects.
For Compliance:
FSSAI require detailed information to be printer on food packaging which can including expiration dates, batch numbers, and manufacturing locations.
For Consumer:
Consumers rely on information before purchasing decisions such as expiration dates, ingredients, and nutritional facts etc.
Now let’s see what the different methods of Marking and Coding are.
Inkjet Printing Machine:
Widely used for its flexibility and ability to print on various surfaces. It is suitable for high-speed production lines.
Laser Coding Machine:
For permanent and tamper-proof solution laser marking machine is the go-to solution. You can mark directly on the packaging material, providing high-quality, precise codes.
Thermal Transfer Overprinting Machine:
TTO marking machines are commonly used for flexible packaging materials like bags and pouches.
With all the above technologies a manufacturer can print variable data, bar code, expiry date, manufacturing date as well as MRP on the product directly.
- Applications
- Line Integrations
- Documents
- Overview
- Bag and Pouch
- Jar, Tin and Can
- Carton
- Case
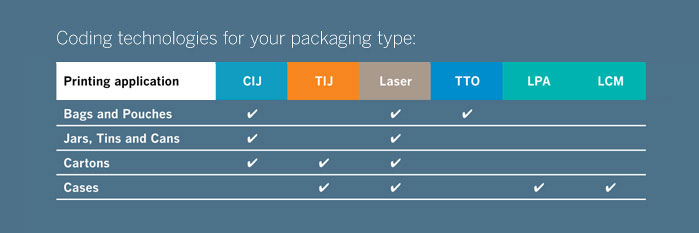

Fluid based, non-contact printing of up to five lines of text, linear and 2D bar codes, or graphics, printed on a variety of packaging types including stationary packaging via traversing systems.

Thermal Transfer Overprinting (TTO)
A digitally controlled printhead precisely melts ink from a ribbon directly onto flexible films to provide high resolution, real-time prints.

Ink-based, non-contact printing using heat and surface tension to move ink onto a package surface. Generally used to print 2D DataMatrix and other bar codes.

Label Printer Applicator (LPA)
Prints and places labels of various sizes on multiple package types.

A beam of infrared light focused and steered with a series of carefully controlled small mirrors to create marks where the heat of the beam interacts with the packaging surface.

Ink-based, non-contact printing of multiple data types (alphanumeric, logos and bar codes) in large sizes primarily used for secondary packaging such as cases.
Solutions for a wide variety of bag types
From pillow to four-sided to block-bottom, bag variety and the machines used to fill them continue to evolve. New bag features and packaging lines can dictate your coding technology selection, but code quality and content requirements also play a role.
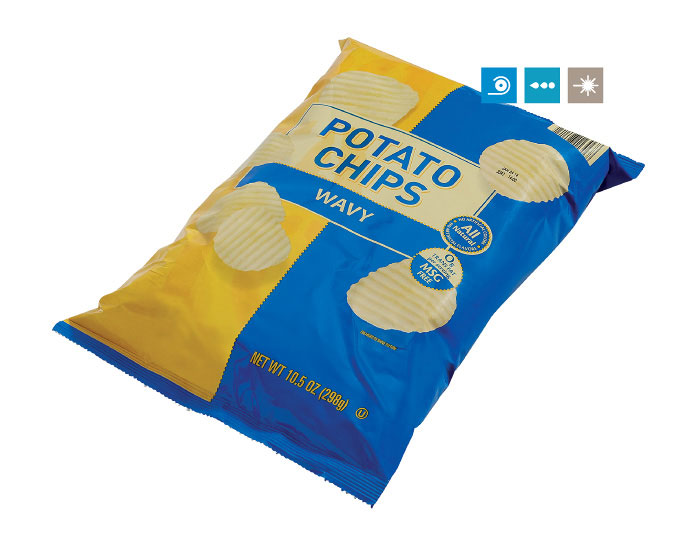
Thermal Transfer Overprinting (TTO)
- produces high resolution codes (300 dots per inch/12 dots per mm) on flexible film with no solvents
- patented clutchless ribbon drive minimizes maintenance-related downtime and maximizes ribbon efficiency
Continuous Ink Jet (CIJ)
- particularly useful for more complicated applications such as preformed pouches and bags with very thick resealable zippers
- CleanFlow™ printhead reduces frequency of printhead cleanings, helping to maximize uptime
Laser Marking Systems
- ideal for pre-printed polypropylene films or a reverse printed Datalase® patch between two layers of a multi-laminate film
- large marking fields help optimize power settings and avoid film burn through
Versatility to code on almost anything
Substrate, environmental considerations or requirements for specialty inks can make selection of a coding solution more challenging. With the right expertise, an optimal solution can be specified for your snack production line.

Continuous Ink Jet (CIJ)
- easy integration onto your line for printing on the shoulder, top or bottom of a wide variety of substrates
- broadest portfolio in the industry at over 175 ink offerings including odorless and non-MEK inks
Laser Marking Systems
- no inks or fluids required, thereby eliminating the potential of ink affecting product integrity
- Videojet fume extraction systems help keep the production environment and marking lens clean
Coding solutions to meet your unique needs
Selection of a carton coding technology is based on the unique needs of your business. Things to consider include requirements for limited consumables, permanent or 2D codes or even solvent-free technologies.
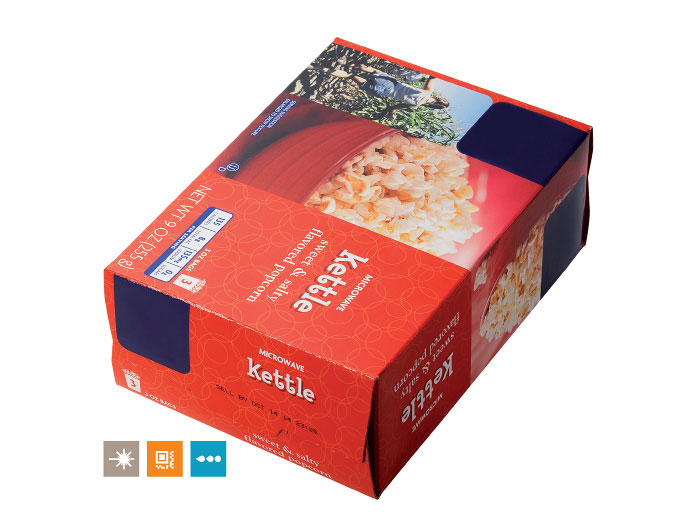
Laser Marking Systems
- ideal for crisp, clear and permanent coding; utilizes virtually no consumables
- comprehensive portfolio of laser accessories including lenses and beam turning units to simplify line integration and maximize laser performance
Thermal Ink Jet (TIJ)
- high resolution, ink-based printing with no wear parts, minimizing maintenance and related downtime
- compact design for easy integration into your line and flexible communication choices for ease-of-use
Continuous Ink Jet (CIJ)
- specialty inks that can create contrast and are ideal for use on virtually all carton materials, including aqueous overcoats and other varnishes
- Smart Cartridge™ fluid delivery system means virtually no mess, no waste, and no mistake fluids replenishment
Empower your supply chain
Legible case coding is the cornerstone of effective inventory management throughout the supply chain. Videojet can help in a variety of ways, providing high resolution printing for direct-to-box and automatic label applications.
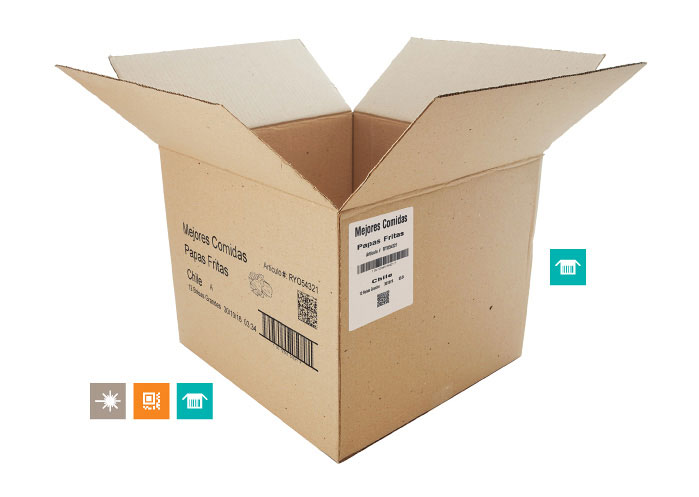
Large Character Marking (LCM)
- eliminates the cost, storage and management of labels and need for customer-specific pre-printed cases
- solution with patented micropurge process purges ink in programmable intervals to help keep the printhead free of debris for best print quality
Label Printer Applicator (LPA)
- automatic application of high quality printed labels offers greater speed, accuracy and error prevention than hand labeling
- designed for ease of use and low maintenance
Thermal Ink Jet (TIJ)
- creates complex, detailed codes ideal for retail ready packaging
- Videojet’s ideal for non-porous substrates, MEK-based inks help ensure good code recovery even after line interruptions
Laser Marking Systems
- a DataLase® coated case marked with a laser will produce a dark black and extremely high resolution print
- especially useful for water-resistant coated boxes, as it enables clear, dark printing without damage to the protective coating
- Vertical Form Fill Seal (VFFS)
- Vertical Filling Line
- Cartoner
- Case Packer and Sealer
Whether intermittent or continuous motion, Videojet has a range of printers to address the growing complexity of VFFS bags and pouches. Packaging features, like zippers and gussets, and the type of VFFS line require a thoughtful selection of the right coding technology.
Integration challenges can be physical, in terms of space and the need for mounting accessories, or communications-based. Videojet Thermal Transfer Overprinter (TTO) products have been engineered by packaging industry experts to make all aspects of interaction from VFFS installation to customer operation as simple as possible. In addition, Videojet’s service and technical support team help ensure that the installation is done right the first time and provides support throughout the life of the printer.
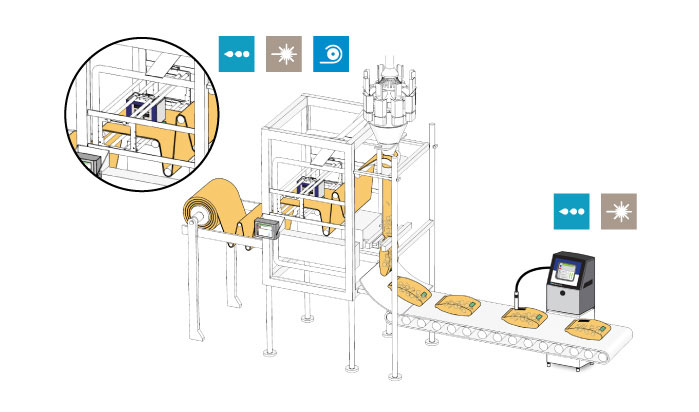

Fluid based, non-contact printing of up to five lines of text, linear and 2D bar codes, or graphics, printed on a variety of packaging types including stationary packaging via traversing systems.

Thermal Transfer Overprinting (TTO)
A digitally controlled printhead precisely melts ink from a ribbon directly onto flexible films to provide high resolution, real-time prints.

A beam of infrared light focused and steered with a series of carefully controlled small mirrors to create marks where the heat of the beam interacts with the packaging surface.
With this application, the printer is typically integrated onto your conveyor after the sealed jar, tin or can has been discharged. Depending on your preferred code location, the printer can easily be configured to print on the bottom, top or shoulder of the container.
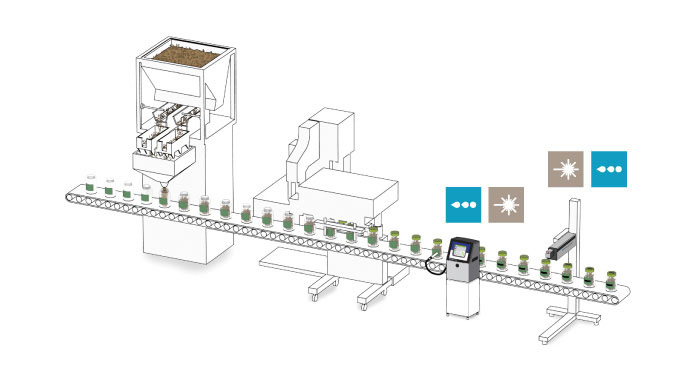

Fluid based, non-contact printing of up to five lines of text, linear and 2D bar codes, or graphics, printed on a variety of packaging types including stationary packaging via traversing systems.

A beam of infrared light focused and steered with a series of carefully controlled small mirrors to create marks where the heat of the beam interacts with the packaging surface.
Several printing options can serve in this application and can be integrated with the machine or immediately downstream in the outfeed. The optimal installation location will depend upon the size constraints of both the cartoner and the preferred coding technology.
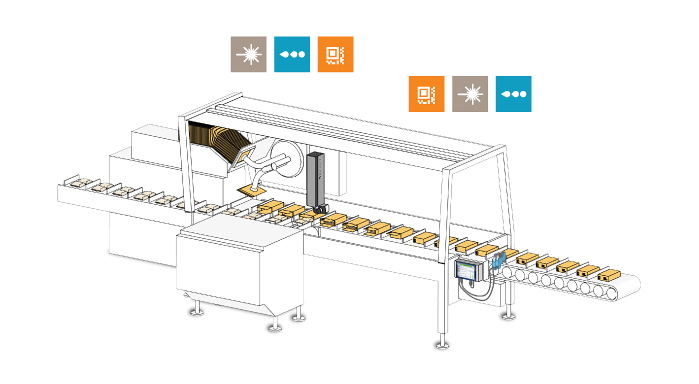

A beam of infrared light focused and steered with a series of carefully controlled small mirrors to create marks where the heat of the beam interacts with the packaging surface.

Ink-based, non-contact printing using heat and surface tension to move link onto a package surface. Generally used to print 2D DataMatrix and other bar codes.

Fluid based, non-contact printing of up to five lines of text, linear and 2D bar codes, or graphics, printed on a variety of packaging types including stationary packaging via traversing systems.
Case printers are best integrated on your conveyor after the sealed case has been discharged. The type and amount of information you want to print on your cases determines which coding solution is ideal for you.
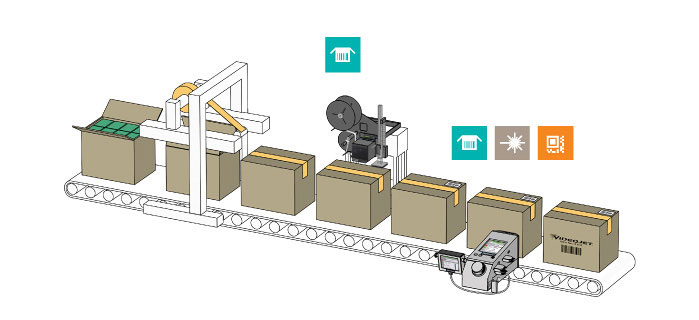

Ink-based, non-contact printing of multiple data types (alphanumeric, logos and bar codes) in large sizes primarily used for secondary packaging such as cases.

Label Printer Applicator (LPA)
Print and places labels of various sizes on multiple package types.

Ink-based, non-contact printing using heat and surface tension to move link onto a package surface. Generally used to print 2D DataMatrix and other bar codes.

A beam of infrared light focused and steered with a series of carefully controlled small mirrors to create marks where the heat of the beam interacts with the packaging surface.
- Brochures
- Application Notes
- Case Studies
- White Papers
Contact Us
Sales and Marketing contact:
9:30 AM – 6:30 PM (Monday – Friday)
Service and Technical support